What Is a Pitman Shift Pattern?
The Pitman shift pattern is a system of shift work commonly utilized to ensure 24-hour operational coverage across various industries, such as law enforcement, emergency medical services, and facilities that require around-the-clock monitoring and presence.
This scheduling model relies on a team-based approach to manage and distribute work hours effectively.
The structure of the Pitman Shift Schedule can be define as:
- Teams work for 2 consecutive days, followed by 2 days off.
- They then work for 3 consecutive days, followed by 2 days off.
- This pattern concludes with another 2 consecutive days of work and is followed by a longer rest period of 3 days off.
The Pitman shift pattern can be fixed or rotating:
- Fixed Pitman Schedule: Teams have a steady rotation, with specific teams always assigned to either day or night shifts.
- Rotating Pitman Schedule: Teams alternate between day and night shifts, providing variability in the work schedule.
Advantages include prolonged rest periods and consistent 24/7 coverage. However, it requires careful administration and planning, often through a calendar specifically designed to accommodate the complexity of the Pitman schedule.
The Pitman shift schedule calendar is crucial for both management and employees to track their work shifts, days off, and ensuring balance in staffing levels.
Further Reading: Shift Patterns
Two Most Common Pitman Schedule Examples
The Pitman Shift Schedule is implemented in two distinct formats: the Pitman Fixed Schedule and the Rotating Pitman Schedule. These patterns are designed to ensure coverage 24 hours a day, seven days a week, utilizing four teams that work 12-hour shifts.
- Pitman Fixed Schedule
In this schedule, each team works a fixed pattern over a two-week period. It follows a cycle of:
- Two consecutive days of work
- Two consecutive days off
- Three consecutive workdays
- Two days off
- Two consecutive workdays
This cycle is fixed, meaning each team permanently works either the day or night shift.
2. Rotating Pitman Schedule
Contrasting the fixed version, the rotating Pitman Schedule sees teams alternating between day and night shifts. The pattern typically adheres to:
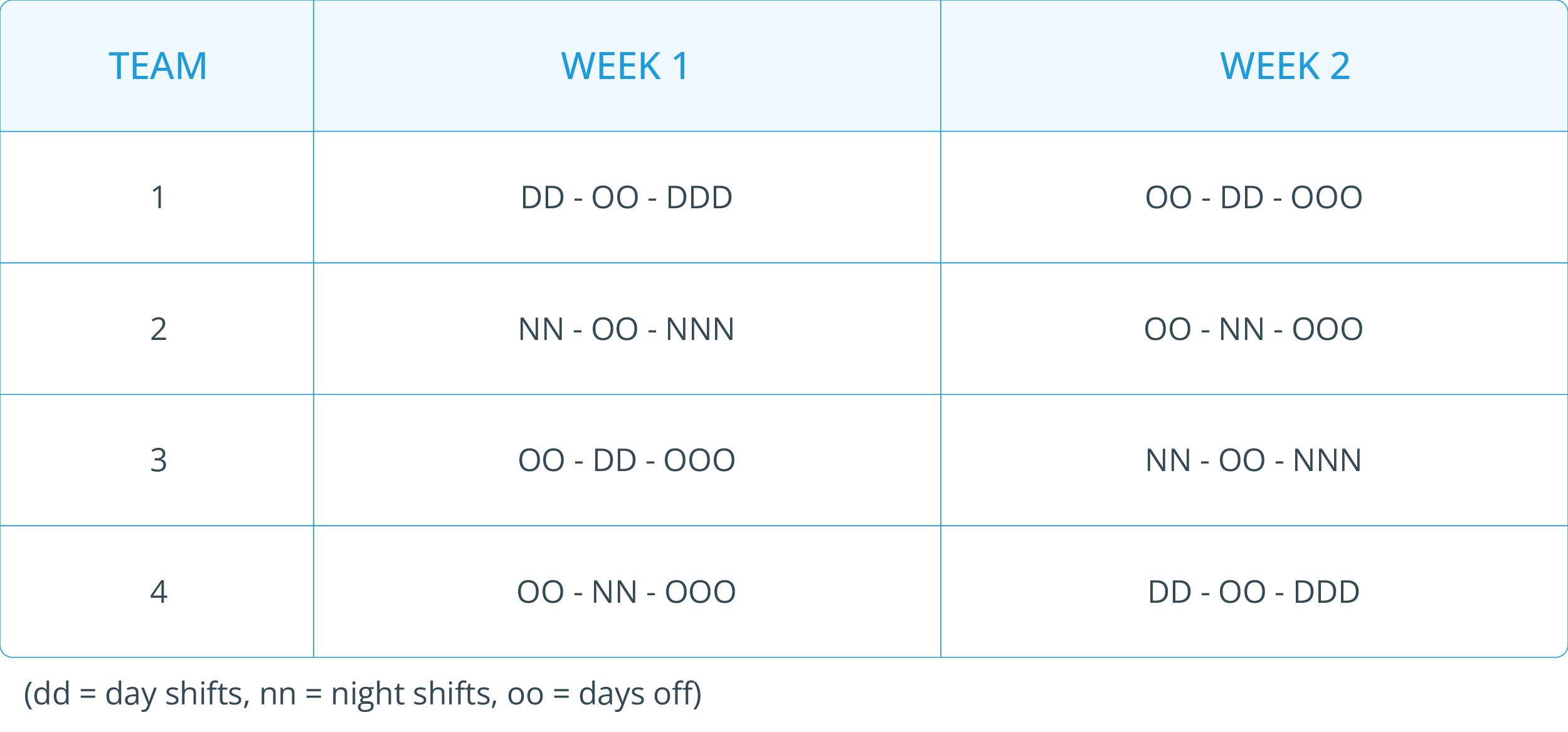
Here, 'D' stands for day shift, 'N' for night shift, and 'O' for off day. The rotation ensures teams do not work more than three consecutive shifts, helping to reduce fatigue.
The core objective of these schedules is to maintain adequate staffing at all hours, maximizing operational productivity while balancing employee work-life balance.
What Industries Typically Use the Pitman Shift Pattern in the UK?
In the United Kingdom, several industries rely on the Pitman shift pattern to maintain continuous operations.
Emergency Services
The Pitman schedule is prevalent among police, fire, and ambulance services.
Constant readiness is crucial, and this scheduling pattern ensures that these essential services remain operational at all times.
Healthcare Facilities
Hospitals and other healthcare providers operate non-stop, with staff working 12-hour shifts to ensure patient care round-the-clock.
Manufacturing Plants:
Industries that require manufacturing processes to continue 24/7 without interruption often adopt the Pitman shift pattern. This includes pharmaceuticals, automotive, and food production sectors.
Utilities
Utility companies, particularly those in the energy sector—power plants and water treatment facilities—utilize this schedule to keep vital services running smoothly without downtime.
Each sector values the Pitman schedule for its ability to balance the demands of 24/7 service provision with employee well-being, ensuring that staffing levels are consistent while allowing for adequate rest periods between shifts.
Further Reading: 24/5 Shift Pattern
Pitman Shift Schedule Pros and Cons
The Pitman shift schedule operates on a two-week cycle, typically with teams working 12-hour shifts, ensuring 24-hour coverage. Its structure varies between fixed and rotating shifts.
Pros:
- Maximized Days Off: Employees enjoy a significant block of days off without the need for vacation time, which can improve work-life balance.
- Extended Coverage: It provides continuous operation for critical services that require 24/7 staffing.
- Overtime Reduction: Due to the built-in extra hours, the need for overtime can be decreased, which may lead to reduced labor costs.
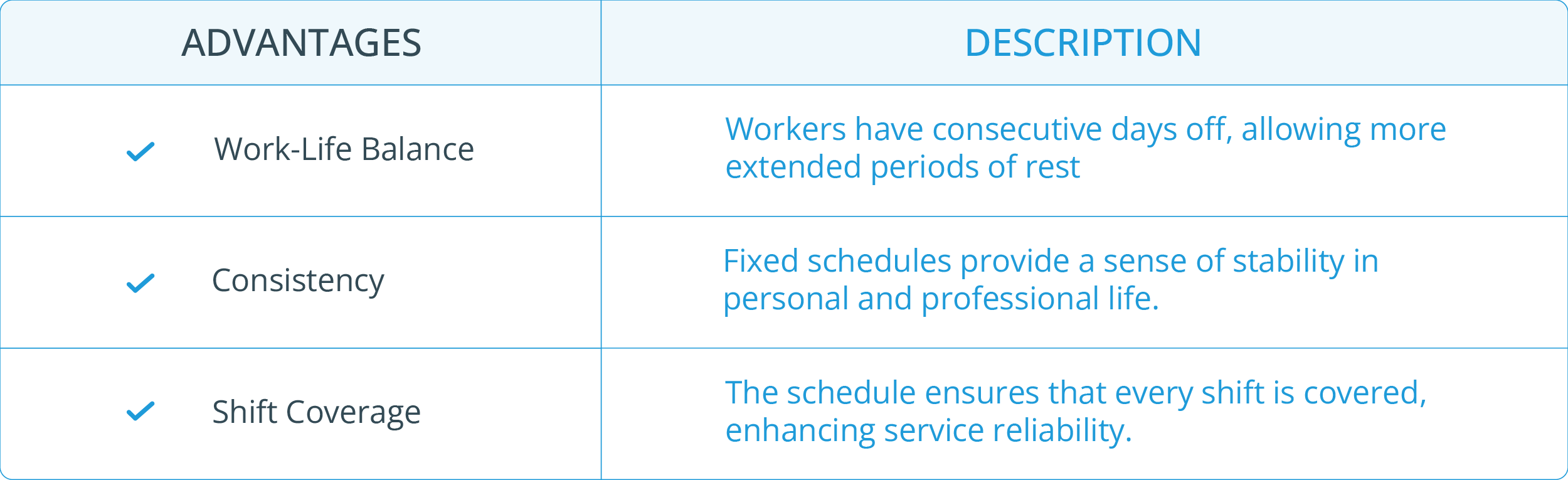
Cons:
- Long Shifts: The 12-hour shifts may lead to increased fatigue and potential burnout.
- Variable Weekly Hours: Workers might find it challenging to adapt to a varying number of work hours each week.
- Work Weekend: The schedule often involves weekend work, which may interfere with social and family time.
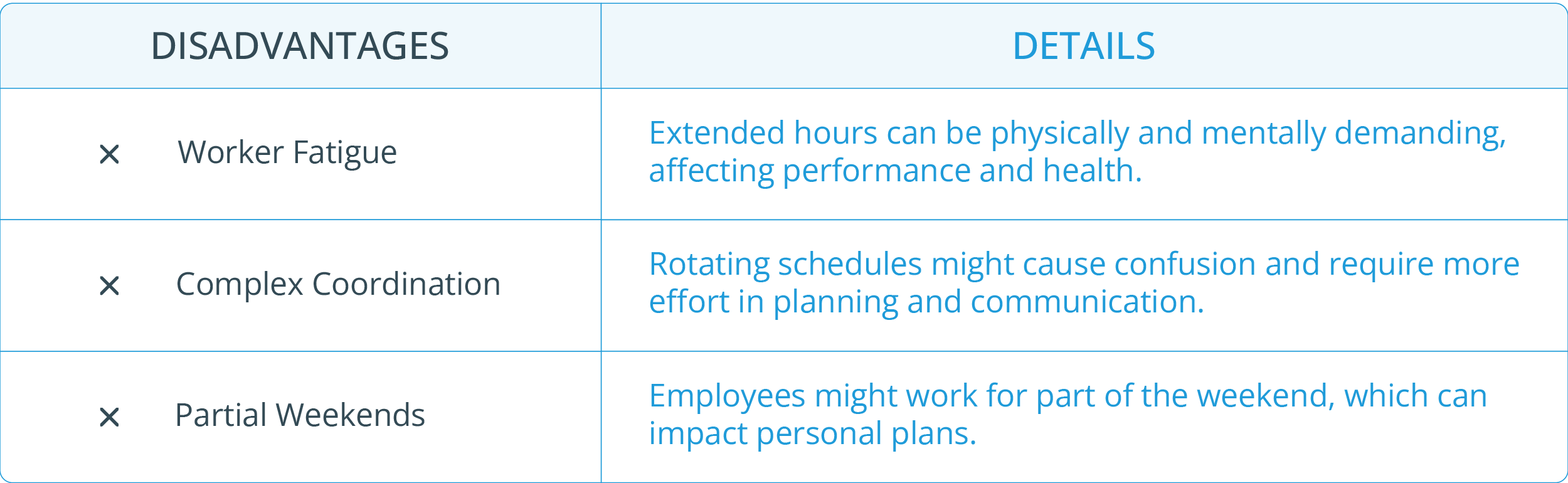
The Pitman schedule has its trade-offs, and organizations considering its application should weigh these aspects against their operational needs and workforce preferences.
How to Implement Pitman Shifts for Your Staff?
Implementing the Pitman shift schedule requires strategic planning to ensure smooth transitions and maintenance of round-the-clock operations. The Pitman schedule consists of 12-hour shifts, covering both day and night, and generally operates on a four-team system.
- Planning Stage
- Assess Suitability: Determine if the Pitman schedule aligns with your organizational needs and employee preferences.
- Schedule Structure: Choose between a fixed or rotating Pitman schedule. A fixed schedule will have teams on a consistent day or night shift, whereas a rotating schedule alternates between day and night shifts.
2. Scheduling Details
- Start and End Times: Establish shift start and end times that support efficient working and employee well-being.
- Transition Periods: Allocate sufficient time for handovers between shifts to ensure continuous operations.
3. Employee Considerations
- Create a shift rotation that allows for an adequate rest period, minimizing fatigue.
- Offer support for employees adapting to night shifts, especially those who may find it more challenging.
4. Technology and Tools
- Utilize scheduling software with time tracking to manage shifts and monitor compliance with work hours.
5. Communication
- Regularly engage with staff to gather feedback and make adjustments as needed.
- Ensure transparency about the schedule structure and expectations.
6. Legal Compliance
- Verify that the schedule complies with labor laws, including overtime regulations and rest periods.
Further Reading: 4 on 2 off Shift Pattern
Key Takeaways on the Pitman Shift Schedule
The Pitman shift schedule is an approach designed to cover 24/7 operational needs with efficiency. It utilizes four teams (crews) working 12-hour shifts over a two-week cycle to ensure round-the-clock coverage.
This system can be found in professions that include emergency services, law enforcement, and facilities that require continuous operation.
Employees benefit from having every other weekend off and no more than three consecutive workdays. Employers appreciate the balance between operational coverage and employee satisfaction. Workers experience adequate rest periods, contributing to safety and productivity.
Despite its complexity, the Pitman schedule can be advantageous for both staff and employers when 24/7 coverage is essential.
FAQs
Why Is It Called the Pitman Shift Pattern?
The Pitman Shift Pattern is named after its creator, presumably an individual or entity with the surname "Pitman." This schedule is tailored for continuous operations requiring around-the-clock staff presence.
What Are the Popular Alternatives to the Pitman Schedule?
Popular alternatives to the Pitman Schedule include:
- 24/48 schedule: Employees work for 24 hours, followed by 48 hours off.
- DuPont schedule: A rotating 12-hour shift pattern designed for continuous operations.
- 4 on 4 off schedule: Workers have four days on duty, followed by four days off.
- 5/8 standard: A traditional 8-hour shift, 5 days a week.
How Many Working Days Are There in a Pitman Shift Pattern?
The Pitman Shift Pattern entails working for 14 days in a 28-day cycle, with each cycle split into two-week periods.
How Many Hours a Year Is the Pitman Shift Pattern?
Employees on the Pitman Shift Pattern work approximately 2,184 hours a year, assuming a standard biweekly schedule of 84 hours.
How Many Weekends Do Employees Work on Pitman Shifts?
In a Pitman Shift Schedule calendar, employees would typically work every other weekend, contributing to the even distribution of shifts.
Is the Pitman Schedule Healthy?
There is no definitive answer as to whether the Pitman Schedule is healthy as it can vary based on individual tolerance and lifestyle. It deploys 12-hour shifts, which may be more taxing but provide longer periods of rest.
How Many Working Days a Month Do Employees Have on the Pitman Shift System?
Employees on the Pitman Shift System work on average:
- 7 days for two 2-week cycles, adding up to 14 working days per month.
- Approximately 42 to 44 hours a week, depending on shift start times and rotation patterns.
This structure ensures coverage while distributing shifts to manage work-life balance.