The term "reasonably practicable" is a legal concept integral to health and safety legislation, commonly used to establish the appropriate level of duty of care in a variety of contexts, from workplace safety to public health.
It denotes the expectation that measures to control risks should be implemented as far as is sensibly achievable, considering the severity of the risk balanced against the difficulty, cost, and practicality of the measures needed to mitigate it.
“Reasonably Practicable” Meaning in Health and Safety: TL;DR
In health and safety regulation, “reasonably practicable” involves a balance between the level of risk and the measures needed to control it against the time, trouble, and expense of taking measures. An employer must weigh the risk against the sacrifices involved in averting it.
“Reasonably Practicable” can be defined in by the following three components:
- Balanced Approach: Employers must consider the likelihood of harm, the potential severity of harm, and the burden of implementing protective measures.
- Cost vs Safety: A measure is not considered reasonably practicable if its cost (in time, trouble, and money) is grossly disproportionate to the risk.
- Risk Assessment: Employers are required to carry out risk assessments to understand vulnerabilities and decide on reasonably practicable steps to mitigate risks.
Employers are legally obligated to ensure health and safety measures are up to the standard of “reasonably practicable.”
Failure to do so can result in significant fines, as evidenced by a manufacturing company in West Yorkshire fined £200,000 after failing to carry out a proper DSEAR risk assessment.
What Does ‘Reasonably Practicable’ Mean?
The concept of ‘reasonably practicable’ serves as a critical standard in health, safety, and risk management, establishing the extent to which one must go to ensure safety and compliance within a reasonable scope that balances risk against resource expenditure.
What Does 'So Far As Is Reasonably Practicable' Mean?
'So Far As Is Reasonably Practicable' (SFAIRP) is a term that implies an obligation to ensure health and safety measures up to a level that is feasible and reasonably achievable. The term denotes a legal boundary where action is required until the point where further measures would be disproportionate to the risk.
- Feasibility: Focus on what can be done practically.
- Proportionality: Balance between the level of risk and the measures necessary to control that risk.
What Does 'As Low As Reasonably Practicable' Mean?
'As Low As Reasonably Practicable' (ALARP) relates specifically to risk management. It describes the requirement to reduce risks:
- To the Lowest Level: Limit potential hazards to a minimum.
- Balance Factor: Compare the risk to the cost (in terms of money, time, and trouble) involved in taking measures to reduce it.
What Does 'As Soon As Reasonably Practicable' Mean?
'As Soon As Reasonably Practicable' indicates a timeframe in which actions should be taken to rectify or address an issue, considering the circumstances.
- Timeliness: Promptness is key, but aligned with what is sensibly executable.
- Contextual Factors: Consideration of current conditions and limitations.
The terms 'as far as is reasonably practicable' and 'as soon as reasonably practicable' echo the overarching principle of achieving the highest level of safety that is reasonably achievable given the particular context of the situation.
Further Reading: Flexible Working Bill
Where Does the Term ‘Reasonably Practicable’ Come From?
The term ‘reasonably practicable’ has its roots in British law, specifically the Health and Safety at Work Act 1974. This pivotal piece of legislation emphasizes employers' responsibility to ensure their employees' safety, health, and welfare to a feasible extent.
The concept embedded within the term involves balancing the level of risk and the measures needed to control that risk, considering magnitude, likelihood, and the resources involved.
Legal precedents have further honed the interpretation of ‘reasonably practicable’.
Courts evaluate actions taken by duty holders against the standard of a reasonable person facing the same legal obligations. This objective assessment demands a rigorous analysis of what steps the duty holder could have reasonably taken to mitigate risks.
It is a term inextricably linked with feasibility; it recognizes that while absolute safety is an ideal, a pragmatic approach to risk management is expected.
The term signals that while some risks can never be entirely eliminated, they must be reduced 'as low as reasonably practicable' (ALARP). This entails implementing measures if they are proportionate to the risk in terms of time, trouble, cost, and physical difficulty.
Reasonably Practicable Example
In the context of workplace safety, reasonably practicable involves a combination of practicality and reasonableness in ensuring the health and safety of employees. An example can illustrate how this principle applies in a real-world scenario.
Imagine a manufacturing company where workers are exposed to the risk of hearing damage due to loud machinery.
The employer assesses the risk and identifies measures that can be taken to protect the workers' hearing. They must then implement these measures to the extent that it is reasonably practicable.
The reasonably practicable measures could include:
- Provision of Protective Equipment: Providing all workers with high-quality ear protection.
- Regular Maintenance: Ensuring machinery is regularly maintained to minimize noise levels.
- Administrative Controls: Implementing shift rotations to reduce each worker's exposure time to the noise.
- Training Programs: Conducting training for workers on the risks of noise and the importance of using protective equipment.
The company must balance the risk's severity against the cost, resources, and feasibility of the measures to mitigate it.
They must take actions that are proportionate to the risk, which means the costlier or more resource-intensive a safety measure is, the greater the associated risk must be to warrant such an expense.
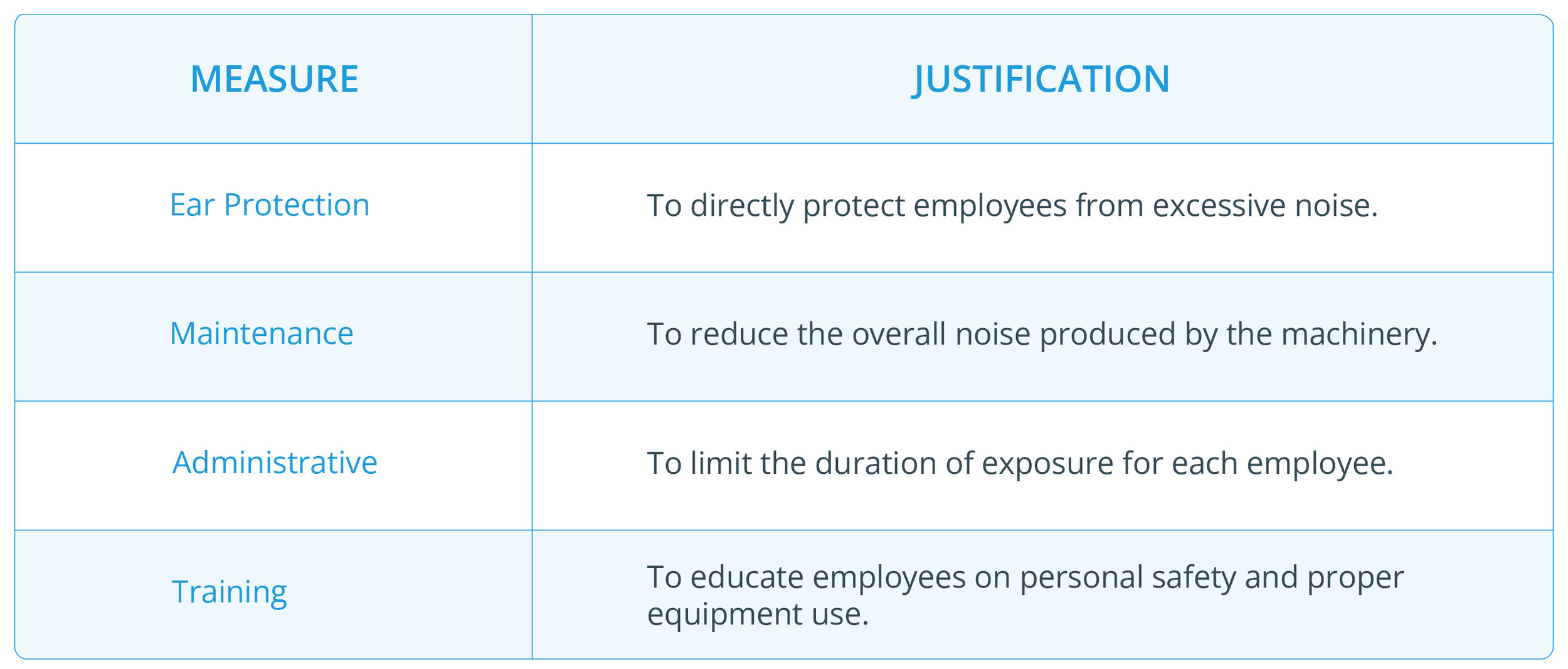
The company’s obligation is not to eliminate all risks but to reduce risks as far as is reasonably practicable. This is a balance that requires regular review as circumstances and technologies change.
Further Reading: Professional References
Who Decides What Is Reasonably Practicable for Health and Safety?
Determining what constitutes as 'reasonably practicable' in the domain of health and safety is an objective process. It involves a standard of behavior that a reasonable person, placed in the duty-holder's situation, would be expected to know and comply with.
Legislation often plays a critical role:
- The Health and Safety at Work Act 1974 (HSWA) lays down duties on employers to ensure health and safety.
- The standard is not absolute; rather, it factors in what is feasible considering the current knowledge, the risk, and the costs of risk mitigation.
In the context of enforcement and compliance:
- Regulatory bodies, such as Health and Safety Executive (HSE) in the UK and similar entities in other jurisdictions, issue guidelines based on this principle.
When disputes arise:
- The judiciary, through case law, shapes the understanding of 'reasonably practicable'.
- Judges consider precedent and the particulars of each case to make determinations.
Employers, therefore, are expected to:
- Assess risks systematically.
- Implement measures to control risks, if they are reasonable.
How to Decide What Is Reasonably Practicable?
Deciding what is reasonably practicable involves a process that considers both the likelihood of harm and the severity of that harm.
It requires an objective assessment where an employer must measure the standard of behavior against what would be expected from a reasonable person in the same situation, adhering to the same duty.
There are key components involved in this decision-making process.
Firstly, one must consider the risk. This involves identifying potential hazards and evaluating the likelihood of harm. One should ask:
- What is the nature of the harm that could occur?
- How likely is the harm to occur?
Secondly, the severity of the potential harm should be assessed. An employer needs to evaluate:
- What are the consequences if the risk materializes?
Following this risk assessment, the duty-holder must review the feasibility of the possible precautions.
Factors to deliberate include:
- The suitability of the available precautions
- The cost associated with these precautions
- The practicality of implementing these measures
Cost should only factor in after the extent of the risk and the effectiveness of the possible measures are established.
If the risk is significant, cost consideration becomes less of a priority.
The duty-holder must balance these aspects:
- Risk of harm
- Severity of harm
- Efficacy of preventive measures
- Costs and practicality of protective actions
The guiding principle is to ensure health and safety as far as possible within the constraints of what is feasible and reasonable in the circumstances. This forms the crux of determining what is reasonably practicable.
Ensuring That Your Control Measures Are Reasonably Practicable
To define reasonably practicable in the context of health and safety, it involves an objective assessment of what is expected from a reasonable person in a similar situation.
Control measures must align with the anticipated level of risk while being feasible in terms of costs and efforts.
Responsibilities for Ensuring Control Measures are Reasonably Practicable
Each duty-holder must ensure, so far as is reasonably practicable, the health and safety of employees under their care.
Implementation should factor in the current industry standards and available technology. Financial considerations alone do not determine what’s reasonably practicable; rather, balancing the level of risk and the measures necessary to control it is crucial.
Further Reading: Drug Testing at Work
FAQ
What Does ALARP Stand For?
ALARP stands for "As Low As Reasonably Practicable." It is a principle in the regulation and management of safety systems, meaning residual risk should be reduced to the lowest level that is reasonably achievable.
What Does SFAIRP Stand For?
SFAIRP stands for "So Far As Is Reasonably Practicable." Similar to ALARP, SFAIRP is used in UK and NZ health and safety law to indicate that risks should be reduced as much as is feasible without disproportionate effort or expense.
Can an Employer Be Prosecuted if the HSE Disagrees with Their Decision on What’s Reasonably Practicable?
Employers may face legal ramifications if the Health and Safety Executive (HSE) concludes that the measures taken were not sufficiently robust given the magnitude of the risk and the means available to mitigate it.
Are Employers Required to Provide Expensive Control Measures if They Don’t Have a Large Operational Budget?
Employers are obliged to implement control measures that are within the means of what is reasonably practicable. This takes into account the scale of the risk in relation to the resources required to minimize it, including financial factors.
What Is the Difference Between Hazard and Risk?
A hazard is a potential source of harm, while a risk is the likelihood of harm being realized and the severity of its consequences. The distinction is critical for assessing and managing safety.
Does Reasonably Practicable Mean Balancing the Hazard Against the Risk?
Yes, determining what is reasonably practicable involves weighing up the level of risk against the time, trouble, cost, and physical difficulty of taking measures to avoid or reduce the risk.
What Is the Manual Handling Act?
The Manual Handling Operations Regulations (MHOR) enacted in 1992 requires employers to manage the risks from manual handling activities.
It mandates avoiding hazardous manual handling tasks where reasonably practicable and assessing and reducing the risk in unavoidable tasks.